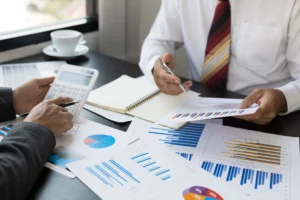
The Business Alignment Model: How to Make it Work for Your Company In 2023
In the early stages of a company, a common pitfall is a vague or ambiguous mission. A plethora of ideas, initiatives, and projects can pull
Every company that buys, sells and/or uses physical products deals with the pains of keeping accurate inventory records. The recent uptick in ecommerce sales, evolving customer preferences and unanticipated supply chain disruptions have converged to make inventory counts especially critical for manufacturers, distributors, wholesalers, retailers and ecommerce companies.
Inventory counts are an integral part of any organization’s internal control environment and tend to be an all-hands-on-deck, manually-intensive affair that take place once a year. The process often extends a week or more, requires operational shutdowns and interrupts fulfillment processes as employees work to count one of the business’ most valuable assets: its physical inventory.
In order to make accurate budgeting, operating and financial decisions, managers and other stakeholders need accurate inventory count data to work with. Publicly-traded companies, for example, must ensure their financial reports are accurate. That means auditors and corporations must perform physical inventory checks before the last day of the company’s fiscal year.
Physical inventory counts are conducted manually, and are therefore both time-consuming and error-prone. When someone has to physically touch or scan inventory during the put-away, inventory check or pick processes, for example, errors are bound to surface. Finding, counting and recording each item is time consuming enough, but the fact that those items might be stored in multiple places throughout the warehouse or storeroom adds even more time to the process. Even when the physical count is completed, rectifying any discrepancies, figuring out what went wrong and then implementing procedures to avoid repeat mistakes takes even more time.
While physical inventory counts are a necessary evil, they needn’t be so significant a burden. This white paper will explore the key inventory count challenges that companies are dealing with now, show how regular, scheduled cycle counting year-round can ease these pains, and discuss how a unified, cloud enterprise resource planning (ERP) solution enables high inventory accuracy year-round.
Any company with a product-centric supply chain likely has anywhere from 20% to 30% of its assets tied up in inventory holding costs (depending on the specific industry). Those holding costs include not only the value of the products themselves, but also the cost of warehousing, controlling and insuring those goods. Ineffective inventory control processes can inflate this percentage, but good inventory management processes can help to minimize these costs.
Up-to-date inventory records provide for better forecasts of sales and purchases and ensure that organizations have the right amount of product on hand to be able to fulfill customer orders, make their own products or both.
Performing a physical inventory count ultimately benefits customers who don’t want to deal with uncertain stock levels in this era of instant gratification. With updated inventory data in hand, companies can fulfill orders promptly, replenish as needed and avoid costly overstock situations. They can also more effectively plan for losses (i.e. due to theft or breakage).
Every day that an item remains in inventory, its value decreases. Over time, the cost to stock the item begins to outweigh its actual value. By using scanners (or other stock-counting technology tools), immediately addressing inventory discrepancies and using inventory management software, companies can improve their counting accuracy and significantly reduce the amount of time required to conduct this vital project.
Other important reasons to perform regular inventory counts include:
Tracking the volume of goods purchased and sold is straightforward in theory but not always easy to master. It also includes inventory turnover rates and actual product purchase costs, both of which can inflate a company’s total inventory investment. Organizations must have enough inventory on hand—and in the right locations—to be able to meet demand while avoiding both stockout and overstock situations.
The biggest headaches of physical inventory counting include the need to manually count inventory—a process that typically requires paper count cards, sheets and pencils. What’s more, some businesses may have limited staff and may need to bring in temporary or part time staff to help deal with the count, adding people unfamiliar with the business and driving up costs. While the required materials may be cheap enough, this approach takes a lot of time, introduces errors and requires a shutdown of the physical facility. Companies can reduce some of this complexity by adding RFID, barcodes or mobile devices to the mix, but even the electronic approach to physical inventory counting requires additional time and resources to complete and is not entirely error free.
And, if not done properly, physical inventory counting not only eats up time, it can introduce errors. Once they’re transferred to the company’s annual financial report and other important statements, these errors can impact the organization’s bottom-line profitability and cast doubt over its stated financial results.
Businesses usually perform their annual physical inventory count before compiling their annual financial reports, but the problem is that performing an inventory count once a year doesn’t always yield the most accurate results. The best way to ease the pain of physical counts is by conducting regular, scheduled cycle counting throughout the year and at predetermined frequencies. These counts can be conducted manually or electronically, using cycle counting or by conducting a full inventory count.
Physical counts can’t be avoided, but there are ways to offset the burden of this annual exercise while saving companies time and allowing them to allocate labor resources to more important tasks. One way businesses can ease the pain of physical inventory counts is by using a process known as cycle counting. Cycle counting is systematic method for counting portions of a company’s stock. As an inventory management option, cycle counting focuses on counting items in a designated area of the warehouse without stopping operations to perform a complete physical inventory. Because of this, cycle counting has become a popular inventory management strategy for companies across all industries. It is often automated and performed at least once per quarter.
With cycle counting, issues can be identified and addressed quickly as they surface, versus just once a year during (or after) a physical inventory count. This helps organizations significantly reduce the amount of time spent on those annual counts—a major competitive advantage in an environment where customers expect orders to ship same-day and arrive within shorter and shorter timeframes.
Businesses that automate cycle counting typically drive faster, more accurate counting. Using RFID and barcodes, for example, is much easier than jotting down stock numbers and/or scanning inventory sheets to find the right item number. Other key benefits of automation include simplified shipping and receiving processes, better visibility over on-hand inventory, better management of missing or stolen merchandise and overall improved inventory management (i.e. less need for “just in case” overstock since your current inventory levels are always right at your fingertips).
Other key benefits of cycle counting include:
Companies with large amounts of stock (e.g. wholesalers, distributors nd that “freezing” stock in order to count inventory to be quite disruptive. As a supplement to these annual inventory counts, organizations can implement perpetual inventory systems that both appease their auditors and effectively reconcile their inventory numbers. While it doesn’t remove the need for a physical inventory county entirely, perpetual inventory systems use point of sale devices and scanners to record inventory changes in real time, making the physical count far simpler. This is important because the operation that shuts down completely for a week in order to count its inventory can find itself behind the competitive curve when it gets back up and running.
Retailers, manufacturers, wholesale distributors and ecommerce companies all have to count their inventory. Whether they use full, annual inventory counts or cycle counting, even companies with small amounts of stock need to know how much they have, which SKUs are languishing on the shelves and which ones need more frequent replenishment.
For example, stock-heavy companies like distributors would benefit from a perpetual inventory system that not only appeases their auditors, but also ensures products are in the right place, and at the right time, when companies need them. Where a periodic inventory system relies on occasional physical counts, a perpetual system continuously tracks inventory balances and automatically updates inventory records when items are sold or received.
An apparel company that has to accommodate frequent consumer preference shifts also needs a robust inventory counting approach, lest it get stuck with too many of “last season’s” garments. Using an upgraded inventory management system, apparel companies can make faster changes to their product mix, track the movements of new items and create space for them on the warehouse or retail floor.
Food and beverage companies and restaurant operators also need good physical counting processes. Dealing with a high volume of perishable goods, these companies have to take regular stock of the goods that are sitting in storerooms and warehouses—specifically those items whose shelf life may be coming down to the wire and ready to spoil.
Even the most organized companies can run into inventory cycle counting challenges. For example, they might unknowingly introduce inventory errors when dealing with multiple locations, or run into issues like paperwork lags and outstanding transactions. When they’re not updated in real time, the counts can also generate false variances that will need to be addressed. To avoid these challenges, companies should clearly define their process, track their inventory accuracy and then aspire to a high degree of accuracy during the process.
When developing a cycle counting program, companies should factor in these three main inputs:
With these inputs in place, companies can use these best practices to create a successful cycle counting approach:
While physical counting once a year may seem like a viable option, cycle counting is less disruptive, provides more visibility into stock daily and can ease the stress of the physical count. By combining an inventory management system and warehouse management system (WMS) with regular cycle counts, organizations benefit from more accurate inventory levels, automatic prompts for items that need to be counted, the ability to categorize items based on volumes or value, improved quality assurance, and higher customer satisfaction rates.
Counting inventory is a requirement for doing business. Regardless of how effective their replenishment, tracking and management systems are, companies must conduct regular checks of actual inventory levels for key items. Keeping an accurate item count can help reduce required safety stock, lower overhead costs and give companies more control over their assets.
Thanks to advanced technology, physical inventory counts have become easier, less intrusive and require less manpower. By replacing Excel spreadsheets or other manual inventory control systems with inventory control software, companies can more efficiently track their stock while reducing human error and saving time and money.
Using an inventory management system also ensures that companies always have the right amount of stock at the right locations to meet customer demand. NetSuite’s inventory and warehouse management solution helps inventory managers track and locate stock at a moment’s notice. The system also includes features such as artificial intelligence (AI), vendor managed inventory (VMI) and mobile device integration. The cloud ERP platform’s inventory count feature, for example, improves inventory tracking and provides increased control over key assets. It also allows companies to categorize inventory based on the volume of transactions and/or value, and enter regular periodic counts of on-hand item quantities to maintain inventory accuracy.
With the mobile app, users can scan bins and items, automatically recording the cycle counts without leaving the floor. This makes auditing inventory less intrusive to daily work and reduces manual errors due to incorrect keying and lag time.
In the early stages of a company, a common pitfall is a vague or ambiguous mission. A plethora of ideas, initiatives, and projects can pull
Today’s business environment is fast paced, hypercompetitive and constantly changing. It’s no place for the rearview-mirror finance and accounting processes of old. Instead, companies are
Collaboration tools are the utensils of the workplace. SharePoint and Teams, for example, each bring unique features to the table. One provides a central location
“I don’t remember where that file is.” “They said that all of the project details are in last week’s conversation. But which conversation?!” “There are